Our highways team have been working within the Lifecycle Framework for over 12 years, enhancing the M25—one of the busiest motorway networks in the country. Committed to continuous improvement, we focus on driving efficiencies, enhancing safety, and implementing innovations that keep traffic moving smoothly. Most importantly, we prioritise the safety of both road users and our teams, ensuring everyone gets home safely every day.
One recent example of this is when are team needed to complete urgent concrete repairs on the Bow Arrow Bridge deck (spanning the railway tracks on the A282 near Junction 1A), we faced a unique challenge. The deck’s dense rebar configuration and low cover ruled out mechanical breaking, while its strategic location near Dartford Crossing meant road closure hours had to be minimised to prevent major traffic disruptions.
To overcome these obstacles, we successfully trialled an advanced robotic hydro-demolition machine—a first for Octavius. Working alongside Gunite Solutions, we deployed the robot under a full traffic management (TM) closure to maximise productivity within restricted working hours. The team successfully completed this trial within one nighttime shift. The traditional method of using a hand-held hydro demolition can remove around 0.75-1.0m3 of concrete in a single shift. However, compared to a Robotic hydro demolition, around 6.5-10.0m3 of concrete can be removed in the same amount of time. Traditional means would have meant the works are not possible to take place in an overnight closure.
We’re delighted that due to our committed to thinking differently, providing innovative solutions and ensuring we delight our customer that we successfully completed this trial, setting a new standard for highways construction works within a busy location and difficult structural designs.
Key benefits
- Improved health and safety
The use of a controlled robotic machine eliminates any health and safety risks workers would be otherwise exposed to using manual hydro demolition – which is typically a high-risk operation.
- Debris contained
With almost all the debris being contained by the robot, any future works of this type can be carried out under lane closures, where time and space may be limited.
- Quieter than traditional hydrodemolition
The robot technology minimises noise impact to local stakeholders and the risk of hearing impairments to operatives.
- Increased productivity compared to standard hydro demolition
The robotic machine allows a greater quantity and quality of work to be completed in constrained time or space (i.e road closures). In the right environment robotic hydrodemolition can be 10 times more productive than standard hydro demolition techniques while improving the overall safety of the works delivery.
Thank you to everyone involved for implementing innovations to drive efficiencies for our customer and helping minimise disruption to road users.
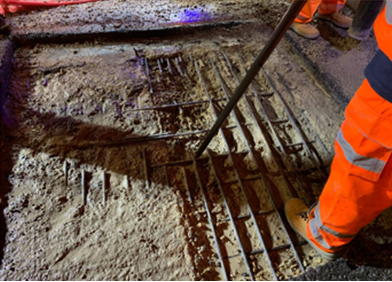
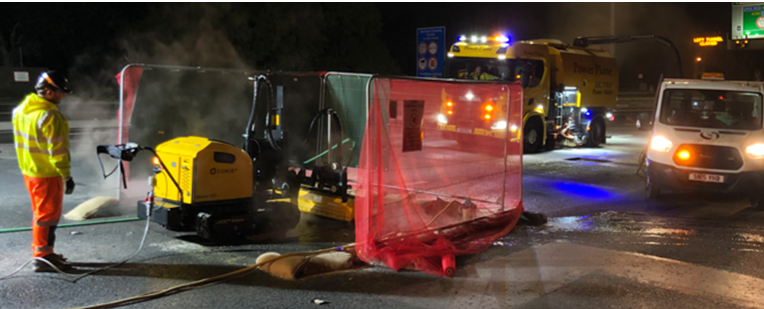